3 Reasons Why AMRs Will Revolutionize Your Supply Chain
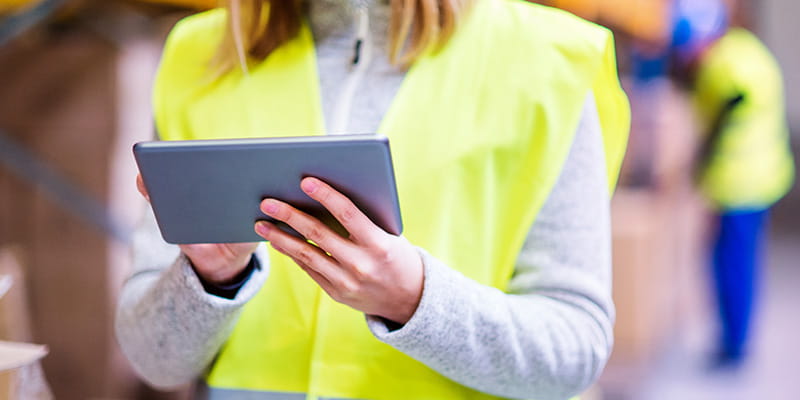
Autonomous Mobile Robots (AMR) are expanding rapidly into material management. With the rise of Industry 4.0, manufacturing data can’t sit still any longer - it must be acted upon instantly. That’s where AMRs come in. These innovative, continuously-connected robots can navigate shop floors with extreme precision. They take the most efficient paths to take your smart factory to the next level.
AMRs are nimble and safe, able to haul hundreds of pounds at a time. Each unit is connected to WiFi and armed with an array of sensors and cameras. These features save employees time and allow managers to recalibrate paths quickly and monitor progress remotely. Let’s discuss the top three ways AMRs will revolutionize your supply chain.
They Save Your Employees Time
Employees can avoid lengthy delivery tasks and instead focus their time on more productive activities. AMRs pick up and drop off pallets, carts, and bins eliminating the need for physical labor. Costs associated with wasted physical movements are drastically reduced. When interfaced with a mobile software like Bossard’s Last Mile Management system, demand for parts is easily triggered. Replenishments can be sent without printing paper picking lists or traveling to other areas of the shop floor.
They Move Independently
AMRs are packed with ultrasonic sensors that allow them to stop, start, and maneuver around obstacles as they transport supplies and materials throughout the shop floor. AMRs can move in all directions and have a full view of the environment. Unlike many traditional robots, autonomous mobile robots do not require wires, beacons, or magnets to guide them. They respond automatically to employee needs via real-time material updates. Relying on digital mapping, each AMR will stay on the most efficient path.
With the help of 3D cameras and lasers, autonomous mobile robots can open doors and gates, move around obstacles, and even ride elevators. Many models are also equipped to shut down or put themselves away during times of emergency. Factory safety compliance increases as fewer people move around work areas, thereby decreasing the potential for work-related injuries and stress.
They Can be Monitored and Controlled Remotely
With the rise of the fourth industrial revolution, customers and executives are closer than ever to production. Robots are monitored and managed from remote locations. Each automated mobile robot is connected to the cloud, delivering a single data point to base executive decisions on – anytime, anywhere. On-board computers continuously communicate material flows and maintenance data to forecast potential issues proactively. Managing the robot fleet is seamless and collaborative, a key innovation in the Industry 4.0 movement.
A crucial part of the material handling process is delivery. By implementing autonomous mobile robots into your supply chain, coupled with you will reduce unnecessary physical movements, move inventory 24/7, and make decisions from a single data set. If your company is considering this type of Industry 4.0 advancement, Bossard would love to consult with you and offers full demonstrations of its smart factory solutions like Last Mile Management, SmartBins, and SmartLabels.